3D Printed Titanium Exhaust Manifold
Additive metal manufacturing is a technology that allows the creation of three-dimensional objects by depositing metal material layer by layer. It also allows the design of parts with complex geometries that would be difficult or impossible to achieve with conventional manufacturing methods.
This technique improves manufacturing finishes. In addition, this method increases the continuity of the surface of the tubes with respect to the traditional method of manifolds made of welded sections. Reducing the number of welded joints ensures continuity on the surface of the duct and eliminates the burrs that may remain from misalignment of assembly and welds. This results in better flow behaviour over the tube, with less flow losses and less drag.
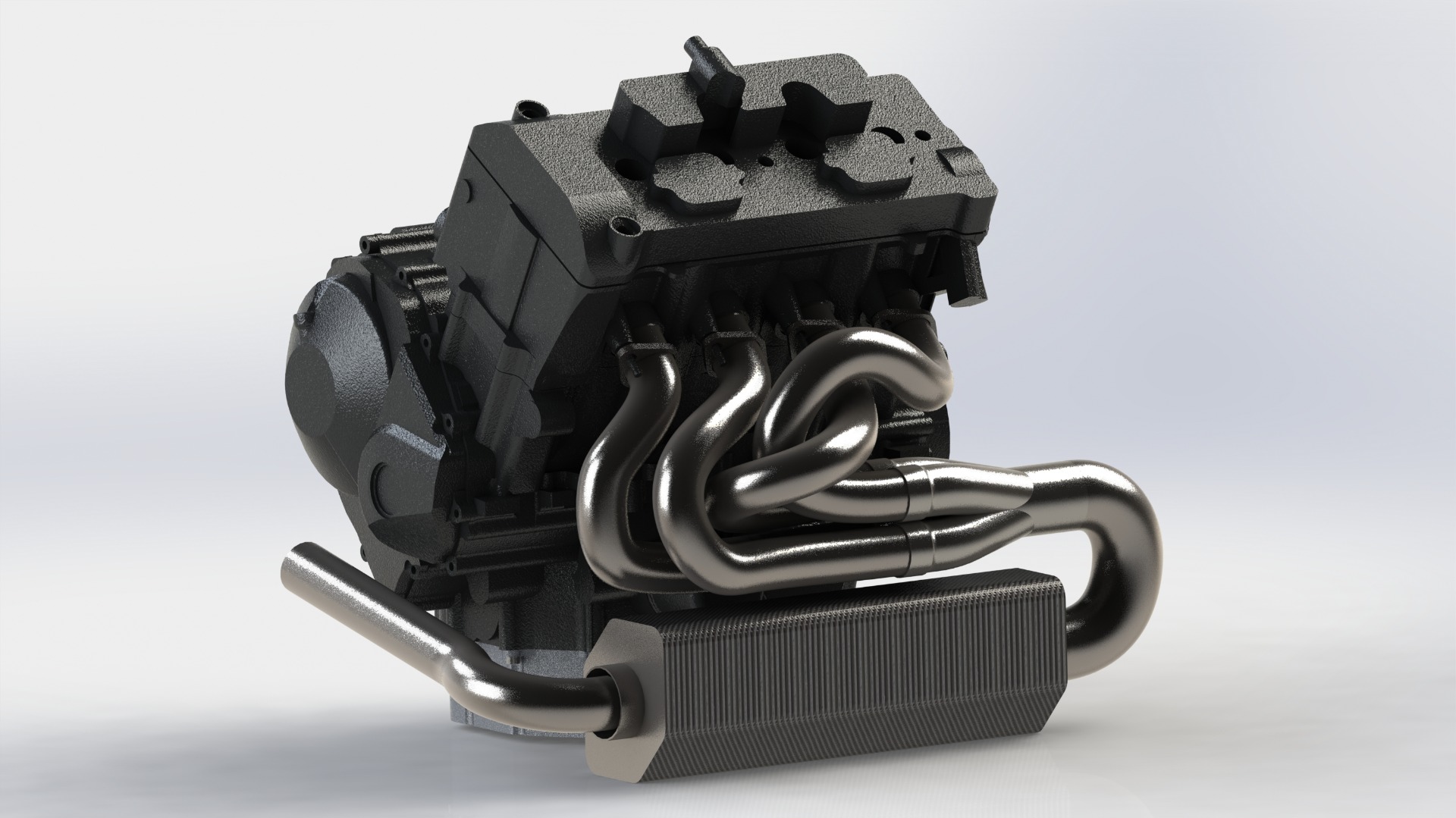
Race car engines powered by sportbike engines usually have a transverse engine layout. This is located at the rear of the driver and in the centre of the vehicle. Usually the transmission is by chain, as in the original motorbike, direct to a differential or shaft. This means that the power output shaft of the engine is parallel to engine output. Thus, the simplicity of the system is maintained.
A new design has been implemented (compared to previous years' designs) which incorporates the 4-1 junction of the manifolds and muffler in the gap between the engine, firewall and driver's seatback. This arrangement of the exhaust system improves the centre of gravity and the distribution of masses on the vehicle, as the exhaust system as a whole represents a high percentage of the mass of the power system due to its materials, dimensions and volume occupied.
The system consists of 3 sections connected by slip joints. The first section is a single piece and corresponds to the 4 manifolds running from the cylinder head to the 4-1 joint. The second piece will be the 4-1 joint along with the elbow that leads to the silencer. The 3rd and last section corresponds to the muffler and the end of the exhaust manifold.
The collectors have an inner tube diameter of 35 mm, while the outlet section will be 50 mm. These tube dimensions, together with the lengths of the headers, match the calculations obtained for the optimal performance of the power system and engine.
The joints of the sections will be fitted with a thermal joint paste between tubes and installation springs to ensure the sealing against air leaks produced by high temperatures, inertias and vibrations.
A different material shall be used. The manufacture of the manifolds in titanium allows to reduce the total weight of the whole system by up to 40% compared to stainless steel or inconel.
Finally, it will be necessary to install a heat retention system to avoid excessive temperature in the surrounding components, as they are located in a poorly ventilated area and surrounded by critical components of the vehicle (fuel tank, electronic power distribution unit, low voltage system battery, wiring, water and oil cooling lines, etc.).
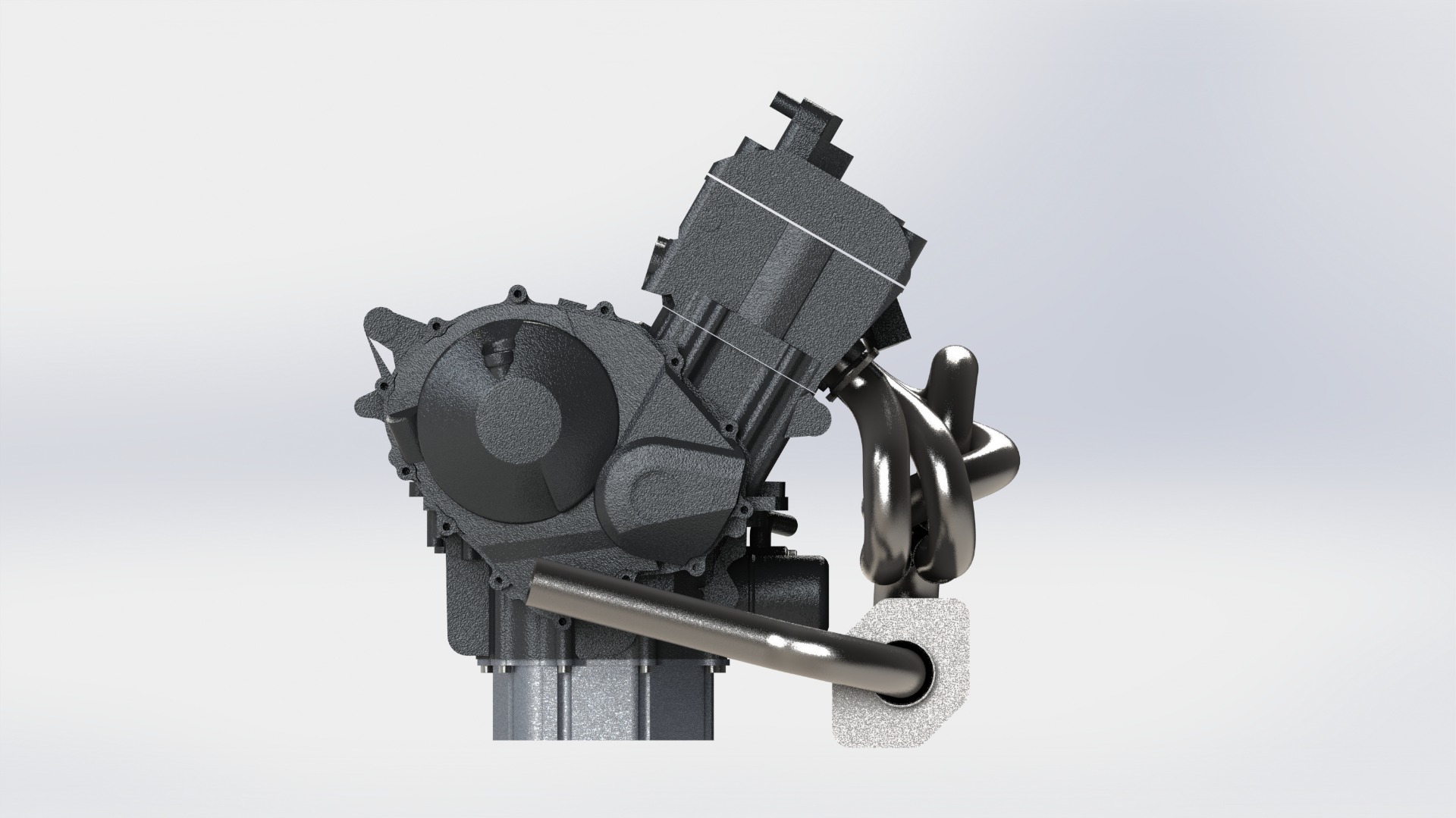
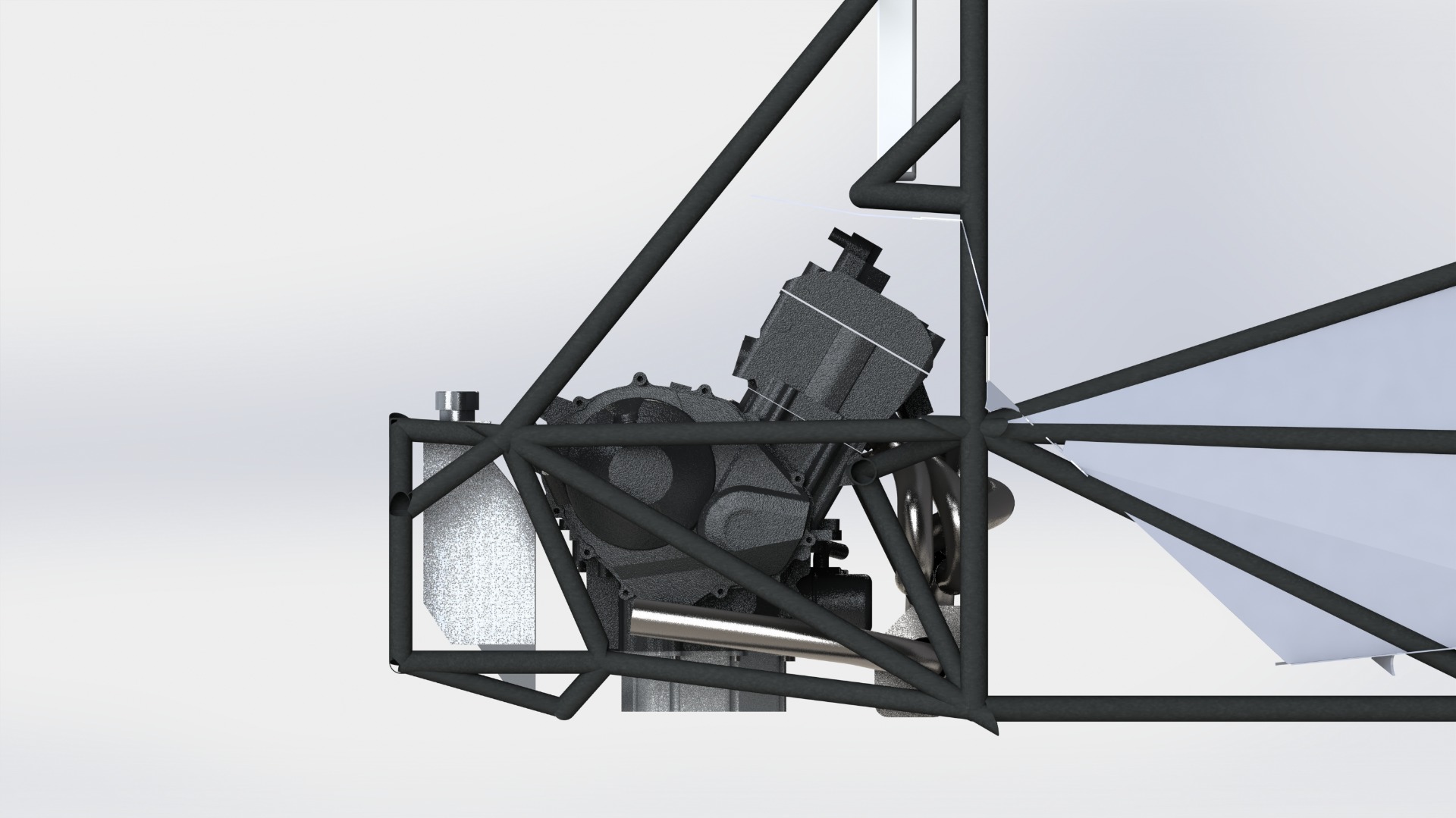